Crafting electric guitars isn’t just about piecing together wood and metal; it’s an art that blends creativity, technical skill, and an ear for music. Each guitar is a unique masterpiece shaped by the hands of skilled artisans.
Ever wondered how much goes into making an electric guitar? It all starts with selecting the finest woods, followed by precise cutting and shaping. The body is then assembled, hardware and electronics are installed, and the finishing touches bring the instrument to life. Finally, an expert luthier fine-tunes the guitar to ensure it produces the perfect sound.
- The Foundation: Wood Selection
- Cutting and Shaping
- Assembling the Body
- Installing Hardware and Electronics
- Finishing Touches: Painting and Polishing
- Fine-Tuning and Testing
The Foundation: Wood Selection
When it comes to crafting an electric guitar, selecting the right wood is paramount. The choice of wood not only influences the guitar's aesthetic appeal but also its tonal characteristics and resonance. Luthiers, the skilled craftsmen who build guitars, spend countless hours seeking out the perfect pieces of wood. Common choices include ash, alder, mahogany, and maple, each offering unique qualities.
Ash, for example, is known for its bright and balanced tone. It's often used for its lightweight properties, making it a favorite for players who perform for extended periods. Alder, on the other hand, provides a full-bodied sound with strong midrange capabilities, contributing to the iconic tones found in many rock and blues genres. Mahogany is celebrated for its rich, warm tones and sustain, making it ideal for genres that demand depth and resonance. Maple typically finds its place in guitar necks, prized for its stability and bright tone.
"The type of wood you select sets the foundation for the guitar's voice," says renowned luthier John Mayer. "It’s like choosing the right canvas before painting a masterpiece."
The age of the wood is also crucial. Seasoned wood, which has been dried and aged, is preferred for its enhanced stability and resonance. This aging process allows the wood fibers to settle, reducing the risk of warping or cracking over time. Moisture content is meticulously monitored throughout the selection process, as excess moisture can lead to long-term issues.
Special Considerations for Tonewoods
In addition to the wood's type and age, other factors such as grain pattern, density, and weight come into play. Luthiers look for tight, straight grains and consistent density, as these attributes contribute to a more predictable and desirable tonal output. The wood's weight is also significant; heavier woods tend to produce a punchier, more focused sound, while lighter woods facilitate warmer and more resonant tones.
Interestingly, environmental sustainability is becoming a growing concern in wood selection. Many manufacturers and independent luthiers are now opting for certified sustainable woods or alternative materials to lessen their environmental impact. This shift not only helps preserve natural forests but also ensures that future generations of musicians can continue to enjoy beautifully crafted instruments.
To illustrate the importance of wood selection, let's consider how it translates to a finished instrument. A luthier might choose a combination of maple for the neck and mahogany for the body to achieve a balanced tone that offers both clarity and warmth. This thoughtful pairing of tonewoods lays the groundwork for the guitar's distinctive sound signature.
Ultimately, the art of selecting wood for crafting electric guitars lies in understanding the intrinsic properties of each type of wood and how they interact with one another. It’s a process that requires knowledge, experience, and an intuitive feel for what will produce the best results. In many ways, the journey of building a guitar begins long before any actual construction – it begins with a deep appreciation for the natural materials that form the heart of these beloved instruments.
Cutting and Shaping
The journey of an electric guitar begins with selecting the finest wood. But transforming this raw material into the sleek, polished body of a guitar is where the real magic happens. This stage, known as cutting and shaping, is where luthiers invest significant time and craftsmanship to lay the foundation for a great-sounding instrument.
First, the selected wood is carefully cut into rough shapes that resemble the final design. This is no easy task; precision is key to ensure the wood sections align perfectly later on. Using templates and bandsaws, luthiers trace and cut the body's outline. Every little detail matters at this stage since even a minor mistake can affect the guitar's sound quality and aesthetics.
Once the rough shape is ready, it’s time for detailed shaping. This step often involves both machine tools and hand tools. Electric routers help carve out cavities for pickups, electronics, and the neck joint accurately. But not everything is left to machines. Hand tools like chisels and rasps are used for finer details and to ensure a smooth finish. The feel of the guitar is crucial, and this is why hand-shaping remains an irreplaceable part of the process.
Renowned luthier John Suhr once said, “You can’t rush art. Let the wood tell you what it wants to be.”
Cutting out the neck is another essential aspect, and it needs to be done with paramount accuracy. The neck's shape and profile are crucial for playability. Modern luthiers use CNC machines to cut the neck with incredible precision. However, they still finish it by hand to perfect the feel and playability, ensuring the neck is comfortable and fits well in the guitarist’s hands.
Various parts of the guitar, like the fretboard and headstock, also begin to take form during this stage. The fretboard, usually made of hard woods like maple or rosewood, is slotted for frets and shaped to the required curvature. The headstock, where tuning pegs will be installed, is crafted to blend seamlessly with the neck. Attention to detail in these parts ensures the guitar will not only sound great but be a joy to play.
Finally, everything needs to be sanded down to achieve a smooth finish. This stage can include multiple rounds of sanding, progressing from coarser to finer grits. This painstaking process removes any tool marks or imperfections and readies the wood for finishing. The smoothness of the wood impacts not just the look but also the guitar's feel and the player's connection to the instrument.
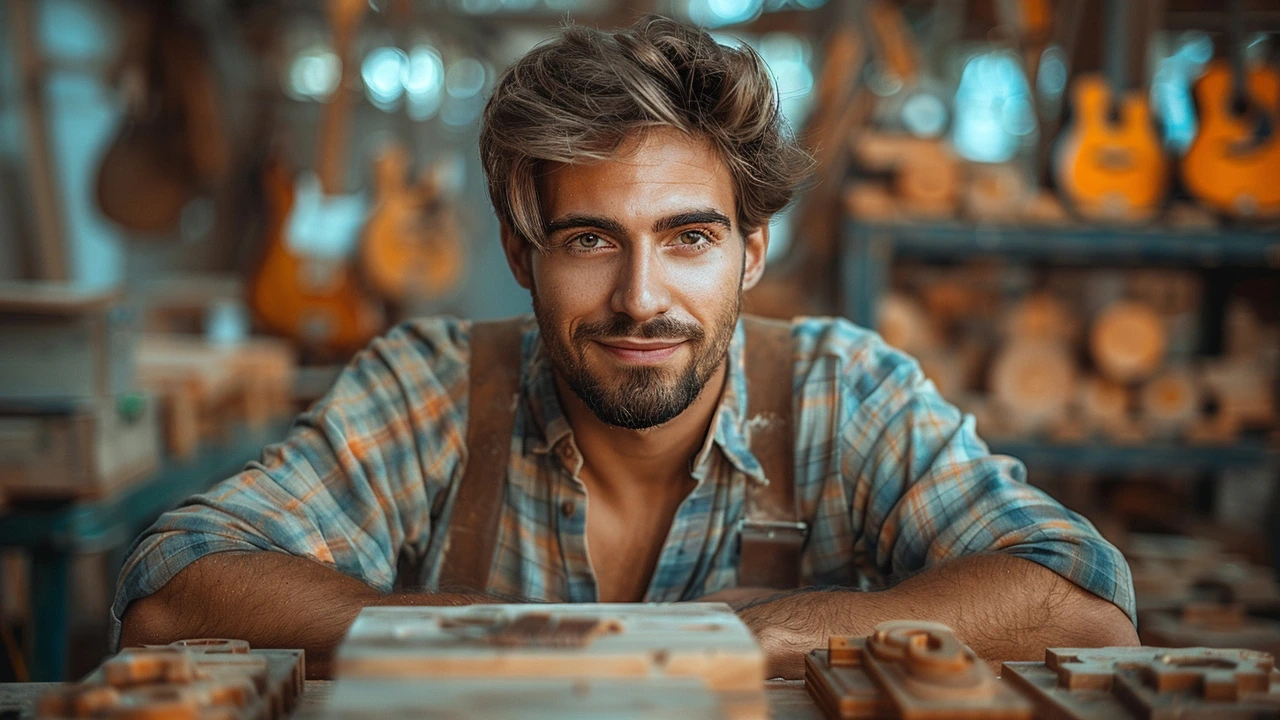
Assembling the Body
Assembling the body of an electric guitar is where the magic truly begins to take shape. This stage is the heart of the guitar-making process, where precision and artistry come together to create an instrument capable of producing hauntingly beautiful music. The journey from raw material to a smooth, resonant guitar body takes patience and an eye for detail.
The body itself usually begins from two or three pieces of high-quality wood, meticulously selected to ensure they match perfectly in tone and appearance. Mahogany, alder, and ash are popular choices, each providing its unique sound properties. These wood pieces are glued together using strong adhesives and clamped tightly to form a seamless bond that will last for years.
Once the glue has set, the next step is carving out the body’s basic shape, often using a CNC (Computer Numerical Control) machine for precision. This machine allows the luthier to follow a pre-programmed design to ensure every curve, contour, and cavity is cut to exact specifications. Following this, hand tools are used to smooth out the edges and add intricate details, making the guitar body a true work of art.
But it’s not just about shaping; internal cavities need to be strategically routed out as well. These cavities make room for essential components like the pickups, wiring, and other electronics. Every millimeter matters, as any misstep can affect the guitar's sound quality and playability. “Creating space for the electronics while maintaining structural integrity is an art in itself,” notes renowned luthier Paul Reed Smith.
At this stage, the neck pocket is also carefully crafted. This is where the guitar’s neck will later be attached, and it has to fit perfectly to ensure the instrument's stability and tone. Any deviation here can lead to playability issues down the line, making this one of the most critical steps in the assembly process.
The body’s assembly wouldn’t be complete without considering weight distribution. A well-balanced guitar is crucial for comfort, especially for musicians who perform long sets. This means sometimes adding or removing material from strategic points in the body to achieve perfect weight distribution while preserving its sonic qualities.
Finally, the joined body goes through a thorough sanding process. Starting with coarse grit sandpaper, the luthier works down to a finer grit. This is an essential step to smooth out any imperfections and prepare the wood for the next stage—finishing. A meticulously sanded body will hold the paint and lacquer much better, leading to a stunning final product.
“The body of a guitar isn’t just an object; it’s the setting for countless dreams and the fuel for endless creativity,” says guitar maker Leo Fender.
Installing Hardware and Electronics
The process of installing hardware and electronics in an electric guitar is where the music really comes to life. This stage involves attaching crucial components like the bridge, tuners, pickups, and control knobs. Precision is key here as even a slight misalignment can affect the playability and sound of the guitar.
First, let’s talk about the bridge. This piece anchors the strings to the body and transfers the string vibrations to the body. Different types of bridges, such as the Fender tremolo or Gibson tune-o-matic, offer unique tonal qualities. Positioning the bridge correctly ensures perfect intonation, which is the first step towards achieving the best sound possible.
Next, consider the tuners, often known as machine heads. These components are installed on the headstock and are essential for keeping the strings in tune. High-quality tuners, like those made by Grover or Schaller, provide stability and make fine-tuning easier, which is crucial for any musician. The placement and alignment of the tuners ensure the string tension is evenly distributed.
"The key to an amazing guitar is in the details. Spend time perfecting hardware placement, and the instrument will sing," says Joe Chambers, a renowned luthier.
Then there's the important role played by the pickups. Pickups are magnets wrapped in coils of wire that capture the string vibrations and convert them into electrical signals. These signals are then amplified to produce sound. Single-coil pickups, like those found in Fender Stratocasters, offer clear and bright tones, while humbuckers provide a warm and thick sound, making them a favorite for genres like rock and metal. Properly mounting and wiring these pickups is essential to avoid unwanted noise and to balance the output levels effectively.
The final components in the electronic setup include the control knobs. These knobs allow the guitarist to adjust volume and tone on the fly. The volume knob controls the overall loudness, while the tone knob adjusts the sound's brightness. Properly soldering the connections and ensuring minimal signal loss is vital for maintaining the guitar's integrity and sound quality.
Once all these components are installed and aligned correctly, the guitar goes through extensive testing. This step is to ensure that everything is functioning as intended. Even the best equipment can face issues like grounding problems or loose connections. A luthier will meticulously test each part and make necessary adjustments. This ensures that when the guitar is finally played, it delivers a seamless, powerful experience.
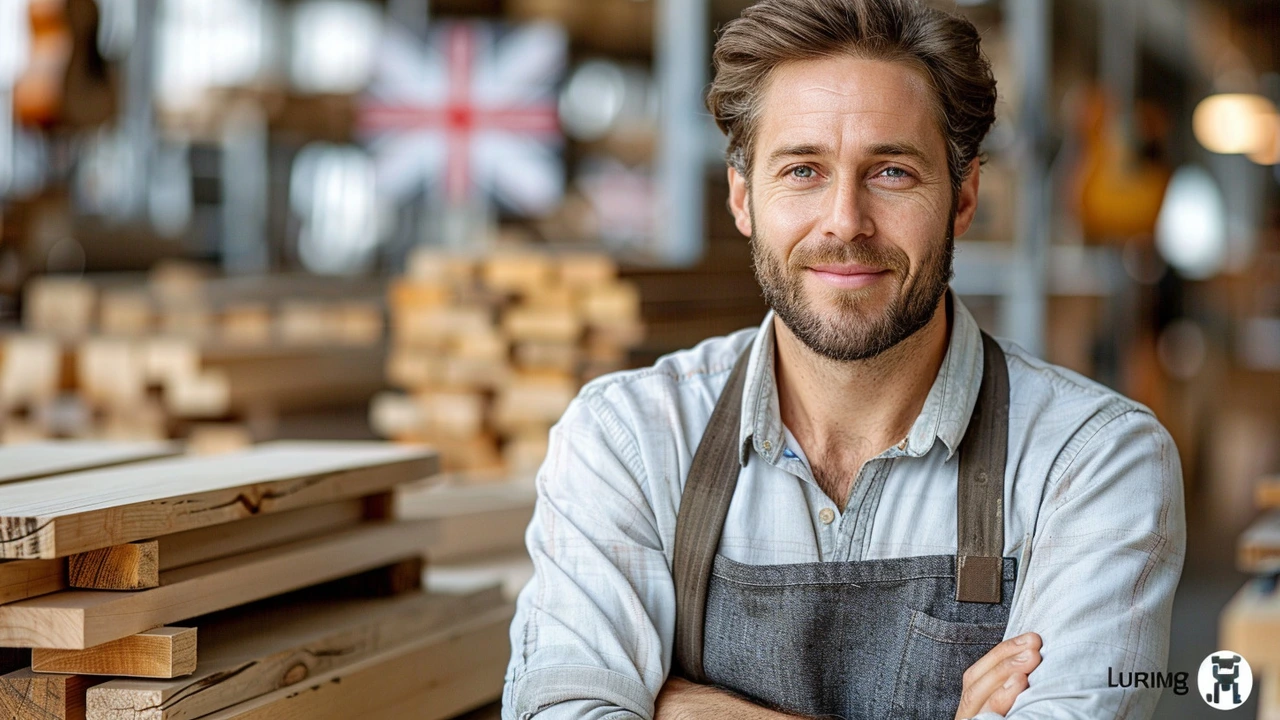
Finishing Touches: Painting and Polishing
This stage is where the guitar starts to show its true colors—literally and figuratively. A well-applied finish not only enhances the aesthetic appeal of the guitar but also protects the wood from moisture and wear.
First, the guitar body is sanded to smooth any rough edges. This process can take hours as it requires meticulous attention to detail. The smoother the body, the better the paint will adhere and look. Next, a primer is applied to create a base for the paint. Primers can be clear or colored, depending on the final hue of the guitar.
Painting an electric guitar isn't just about picking a nice color. It involves multiple layers of paint and clear coats. Each layer must dry completely before the next is applied, which can take time. This patience ensures a depth and richness in the color that you can't get any other way. Once all layers are applied and dry, the body is polished to give it a glossy, professional look.
The importance of a good finish can't be overstated. Not only does it make the guitar look stunning, but it also plays a role in the instrument's tone. A quote from renowned luthier Paul Reed Smith perfectly captures this:
"The finish on a guitar is like the skin on a human. It needs to be perfect, because it's what everybody sees first."
After the paint and clear coat are applied, the guitar undergoes the final polishing phase. This involves buffing the surface to a mirror-like sheen, and it can take several hours. Skilled luthiers often use a combination of hand and machine polishing to achieve this result. The products used during this stage are specifically made for guitars and help to bring out the natural beauty of the wood while ensuring a durable finish.
Once polished, the guitar body is inspected thoroughly to make sure there are no imperfections. Even the smallest flaw can detract from the guitar's beauty and value. If any imperfections are found, they are corrected before moving on. It's this obsessive attention to detail that sets high-quality, handcrafted guitars apart from mass-produced models.
Fine-Tuning and Testing
The journey of creating an electric guitar culminates at the fine-tuning and testing stage. This is where the magic truly happens, transforming a beautifully crafted instrument into one that can produce the sounds musicians crave. Expert luthiers delicately adjust the guitar’s settings to ensure optimal performance.
First, the guitar is strung with precision, often with a preferred brand that complements the guitar's intended use. Once strung, each string’s tension is meticulously adjusted to achieve the right pitch. This isn't just a quick twist of pegs; it requires an intimate understanding of how the guitar will respond to various tension levels.
Then, the luthier moves on to checking and adjusting the neck. The neck's curvature, known as 'relief,' plays a crucial role in the guitar’s playability. A perfectly adjusted neck will feel just right in the hands of the player. Too much bow, and the strings will buzz against the frets; too little, and the strings might feel unresponsive. Each tweak brings the instrument closer to its ideal state.
"The joy of hearing that first perfect chord strummed on a freshly tuned guitar is unparalleled," says renowned luthier John Suhr. "It’s the culmination of hours, sometimes days, of detailed work."
Intonation is the next critical step. Using a strobe tuner, the luthier ensures that the guitar plays in tune across the entire fretboard. This involves fine adjustments to the bridge saddles. A guitar with perfect intonation sounds harmonious even when playing complex chords at high frets. This meticulous process ensures that each note rings true.
The luthier then tests the guitar’s electronics. Each pickup is scrutinized for clarity and balance. Switches and knobs are adjusted to ensure smooth operation. Any unwanted buzz or hum is tracked down and eliminated. The goal is to ensure that the electronics faithfully translate the guitar’s rich tones without introducing noise.
Playability tests follow, giving the guitar a final shakedown. This includes trying out different playing styles, from gentle fingerpicking to intense strumming. The guitar must respond well to all variations. These tests also help identify any last-minute adjustments that might be needed. The tactile feedback from the guitar is pivotal, as it impacts how a guitarist interacts with their instrument.
Every detail is examined closely, and nothing’s left to chance. It may seem like overkill, but these final stages are what set a high-quality guitar apart from the masses. Every guitarist knows the euphoric feeling of playing an instrument that feels just right, and it’s the fine-tuning and testing phase that makes this possible.